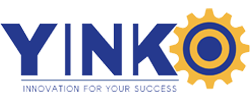
As consumers increasingly demand sustainable and customizable packaging solutions, paper cups have become an integral part of the food and beverage industry. There are technical specs and machines behind these common items. Whether you’re starting a new paper cup manufacturing operation or trying to improve an existing line, it’s important to understand how to choose the right materials, equipment, and designs.
This article will cover some key topics in paper cup production, including how to confirm cup sizes and select the appropriate sealing technology.
When it comes to paper cups, size is more than height and diameter. Several details affect production efficiency and end-user satisfaction.
• Cup Bottom Depth & Angle: These affect how cups nest inside one another, impacting stacking height and packaging.
• Rim Curl and Top Diameter: These directly impact lid fit and overall cup strength.
The most important factor, however, is what the market wants. A cup size that works well in one country may not be acceptable to consumers in another. At YINKO Machine, we tell all our customers to get us cup drawings or actual cup samples so our experienced designers can verify dimensions and create technical drawings for molds. This helps ensure the cups you produce will meet manufacturing requirements and be acceptable to the marketplace.
![]() |
The paper material you select is important for a variety of reasons, including the durability of the cup, how it feels in a person’s hand, and whether it works well with hot and cold drinks.
• Most paper cups are made with paper that is coated with PE. PLA coated paper is enjoying wider acceptance now because of heightened environmental awareness.
• Single PE: minimum 18 g/m²
• Double PE: typical 18/12 g/m²
• When it comes to paper cups, think of thickness, not base weight. Mold tolerances are usually ±0.02 mm.
• Cold Cups: Usually made with double PE coating because of the need for moisture protection.
• Hot Cups: Usually made with single PE coating.
• Larger cups (12 oz. – 16 oz.) typically require thicker paper (0.31 mm – 0.41 mm). Thinner paper can be used, but it changes the way the cup feels in a person’s hand.
Areas of the country or world have preferences for thicker paper. For example, the demand in Europe and North America is for thicker paper and large cup sizes.
Choosing the right paper helps you run production smoothly and cost-efficiently and increases the likelihood that your customers will be satisfied.
![]() |
One of the key decisions you need to make in paper cup manufacturing is whether to use ultrasonic sealing or hot air sealing technology.
• Normal output is 80 cups/min. unless you are using a high-end system.
• Recommended in applications where you regularly change paper or have variability in paper thickness.
• Offers more flexibility with content material.
Hot Air Sealing
• Preferable when production conditions are stable.
• Achieves a higher production speed and consistent performance.
• Accepted for most paper cup lines in current commercial use.
In summary, if you have variety in your material sources or need flexibility, ultrasonic is the way to go. If you don’t, hot air sealing is the preferred way to go for efficiency and reliability.
Most paper cups, especially ones used for beverages, need to fit plastic lids. If the lids don’t fit well, leaks, spills, and unhappy customers will result. YINKO Machine always asks customers to send lid samples to us before we verify cup sizes. Our designers then take measurements to confirm dimensions to facilitate a final cup design that matches the lid so it seals well and looks professional.
![]() |
To keep production flowing, you must do regular maintenance on the paper cup machines. At YINKO Machine, we build our paper cup machines to last over 15 years. However, that depends on the maintenance you do (which should include the following schedules.)
• Weekly: Basic cleaning, oil levels, and visual inspection.
• Monthly: More thorough checks of mechanical parts and moving assemblies.
• Yearly: Complete checks, possibly including part replacement and performance tuning.
Some of the routine maintenance can be done by operators, but most of it should be done by trained technical personnel to ensure long-term stability and to avoid expensive downtime.
Making paper cups is much more than just forming paper into a cylinder. Every decision you make about cup size, paper type, sealing technology, lid fit, and machine maintenance impacts your ability to manufacture them efficiently and market them effectively.
At YINKO Machine, we strive to support our customers in all aspects of this process. Each machine and design we create will continue to meet your technical needs, as well as fit the current marketplace and environmentally sound practices.
Are you ready to start or upgrade your paper cup production line? If so, please contact us today to discuss how we can customize our solutions to meet your needs with innovative, reliable, and environmentally responsible manufacturing.